Un centro de distribución es una instalación logística con un objetivo muy claro: llevar a cabo procesos de recepción y expedición de mercancía para poder suministrar, ágil y eficazmente, productos y mercancías a los clientes finales: ya sean otras empresas, o bien consumidores y usuarios.
La función principal de un centro de distribución es gestionar, del mejor modo posible, el flujo de materiales. Para lograr la máxima eficacia es fundamental dividir y organizar la instalación en diferentes áreas.
Zonas y áreas de un centro de distribución
No existe una única forma de distribuir y organizar un centro de distribución, aunque la mayoría de ellos se organizan siguiendo un esquema similar a este:
Zona de recepción
- Área de control de calidad. Es el lugar donde se lleva a cabo la recepción y el óptimo funcionamiento de todos los elementos implicados, tanto de maquinaria como de software: carretillas, Software de Gestión de Almacenes (SGA), códigos de barras, etc.
- Área de clasificación. Organización de los productos según su lugar de destino.
- Área de adaptación. Es el lugar donde, en función de las diversas necesidades, se realizan cambios de etiquetas, packaging y otras características de los pedidos.
Zona de almacenamiento
- Área de baja rotación. Clasificación del stock según la clasificación ABC, Ley de Pareto 80/20 u otros sistemas.
- Área de alta rotación. Creación de áreas específicas de almacenamiento.
- Área de productos especiales. La normativa obliga a ubicar en lugares apartados, y en ocasiones con medidas de seguridad adicionales, las consideradas Mercancías Peligrosas (ADR) y los productos químicos (APQ). Estos últimos no pueden, por ejemplo, colocarse junto a productos de consumo, como los alimentos.
Zona de selección y recogida de mercancías.
- Es el espacio donde se recepcionan los materiales, se seleccionan y se preparan para poder ser distribuidos.
Zona de reposición de existencias
- Suelen ser zonas de almacenamiento mixto para poder efectuar la reposición sobre la alta rotación o las roturas de stock.
Zona de preparación de pedidos
- Áreas integradas: Picking en estanterías con diferentes grados de automatización.
- Áreas de separación: Picking manual realizado por los empleados.
Zona de expedición
- Área de consolidación. Se preparan las rutas en función de los destinos.
- Área de embalajes. En estas zonas se realizan tratamientos específicos de hiperprotección o paletizaciones especiales para preservar la mercancía de robos o golpes.
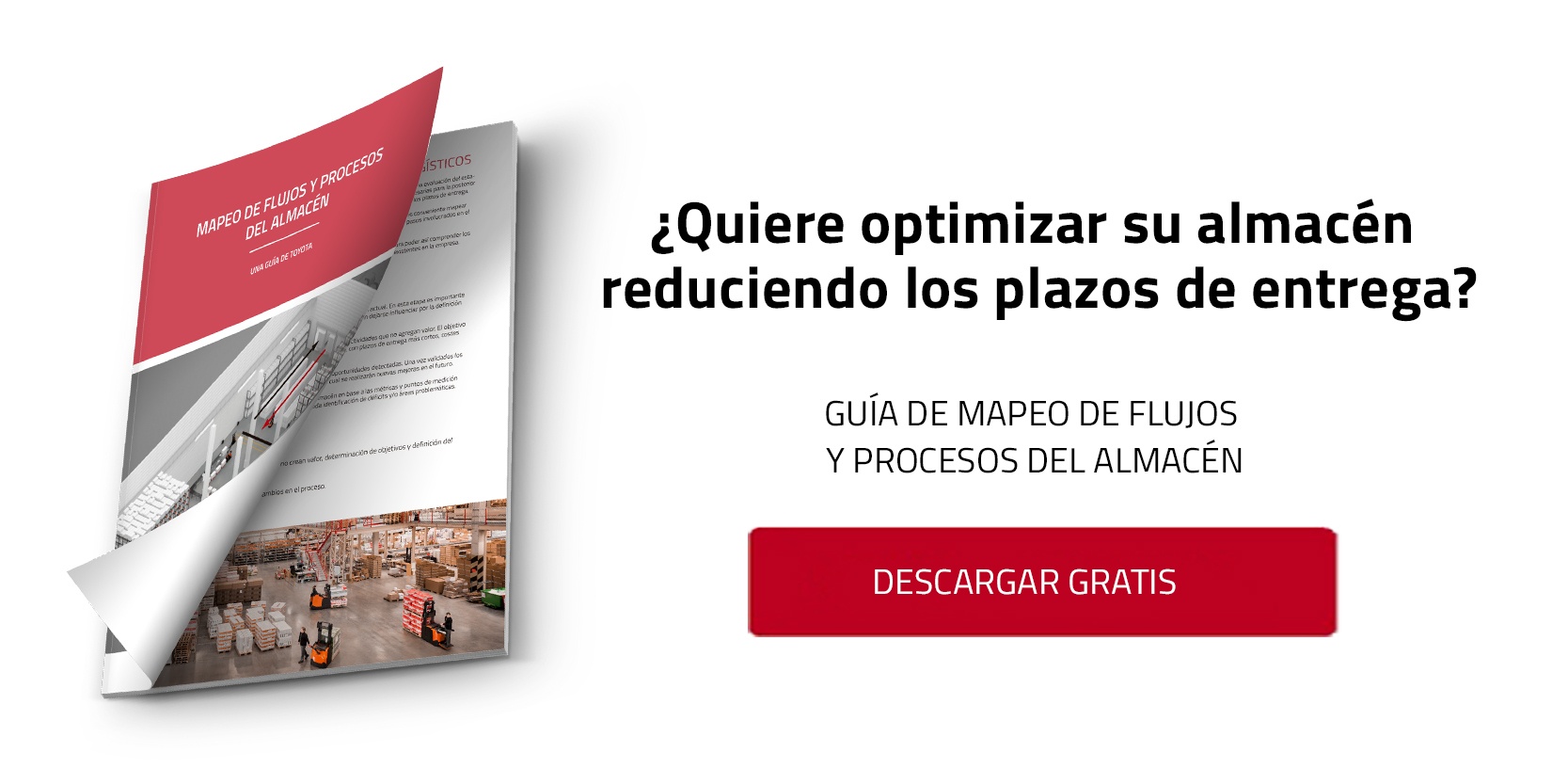
Zonas auxiliares
- Área de devoluciones. Se lleva a cabo la logística inversa.
- Área de envases o embalajes. En ocasiones se realizan cambios en el envoltorio y protección de los productos usando criterios de reciclaje, reutilización y revalorización.
- Área de materiales obsoletos. Las mercancías que salen fuera del catálogo han de ser destruidos.
- Área de oficinas o administración. Es un área común en muchos negocios.
- Área de servicios. Un ejemplo serían las salas especiales para las baterías de los elementos de manutención.
Cómo organizar las distintas zonas de un centro de distribución
La organización, junto con el diseño adecuado de las instalaciones de centros de distribución y de almacenes suponen las siguientes ventajas:
- Lograr un adecuado flujo de materiales.
- Mejorar el servicio al cliente.
- Lograr unas condiciones óptimas de trabajo.
- Minimizar los costes.
Etapas de la distribución de un centro de distribución
La distribución física de un almacén puede dividirse en cinco etapas fundamentales, estas son:
- Determinar las ubicaciones de existencias y el sistema de almacenamiento: FIFO, LIFO MIFO, etc.
- Establecer el sistema de manejo de materiales. Puede ser hombre-producto (el empleado va a buscar el artículo) o producto-hombre (el producto se dirige de forma automática al empleado, que está parado en un lugar fijo). Obviamente, el sistema elegido condiciona los elementos de manutención necesarios.
- Mantener un sistema de control de inventarios. Los SGA actuales proporcionan todo tipo de información, entre ellas la ubicación de los distintos pedidos en cada momento.
- Establecer procedimientos para tramitar los pedidos. Existen cuatro tipos diferentes de combinaciones y cada una de ellas se gestiona de un modo distinto: 1) un pedido-un hombre, 2) un pedido-varios hombres, 3) varios pedidos-un hombre y 4) varios pedidos-varios hombres.
- Seleccionar el medio de transporte. Camiones, furgonetas, avión, barco, etc.
Principios de la distribución en planta de un centro de distribución
Existen una serie de principios que deben seguirse en el momento de realizar el layout o la distribución en planta de un almacén:
- Los artículos de más movimiento deben ubicarse cerca de la salida para reducir el tiempo de desplazamiento.
- Siempre hay que tratar de minimizar el trabajo manual. Por ejemplo, colocando los artículos pesados y difíciles de transportar en aquellos lugares en los que sea más sencillos desplazarlos y almacenarlos.
- Los materiales inflamables y peligrosos o sensibles al agua y al sol deberían almacenarse en algún anexo, normalmente en el exterior del edificio del centro de distribución.
- Dotar a los artículos que lo requieran de separaciones y/o protecciones.
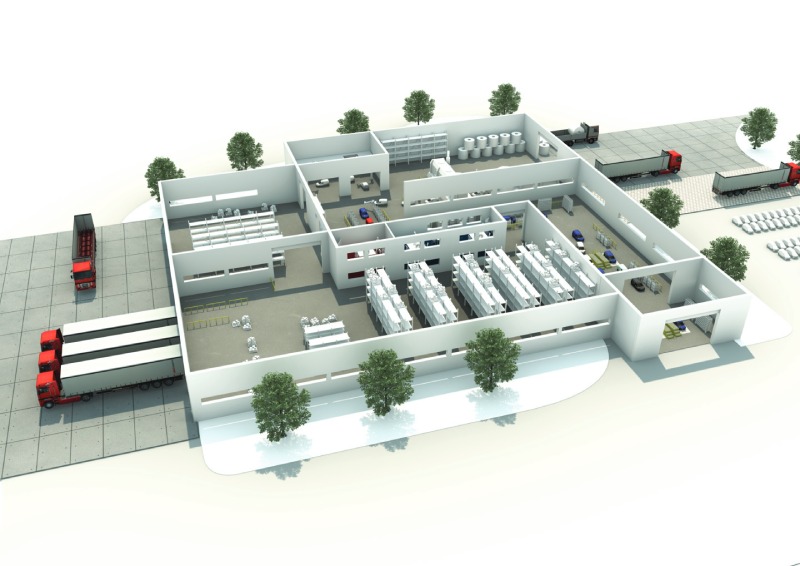
10 claves para optimizar el flujo de materiales
- Los flujos de materiales deben condicionar el equipamiento a utilizar y no al contrario.
- Valorar la carga máxima de los medios de transporte externos, así como de los elementos de manutención.
- Calcular el tiempo necesario para cada operación.
- Tener en cuenta las características de las materias primas y productos a almacenar: tamaño, peso, fechas de caducidad, etc.
- Analizar y tener en cuenta aspectos relacionados con los productos: nivel de rotación, cantidad de productos suministrados, frecuencia y complejidad de los pedidos, etc.
- Aprovechar eficientemente el espacio disponible, tanto m2 como m3.
- Utilizar los elementos de manutención (carretillas retráctiles, contrapesadas, transpaletas…) que mejor se adapten a las características del centro de distribución y los materiales almacenados.
- Tener un perfecto control de las mercancías, el stock y el inventario, usando para ellos las mejores herramientas informáticas, SGA, CRM.
- Apostar por la transformación digital.
- Asesorarse correctamente y valorar la implementación de sistemas de automatización e, incluso, de robotización del centro logístico.
La importancia del layout
El layout hace referencia a la disposición y distribución en planta de los elementos del almacén. El diseño del layout de un almacén debe asegurar el manejo eficiente de los productos y materias primas.
Otro aspecto clave es poner en marcha una buena estrategia de entradas y salidas de los productos del almacén, eligiendo la más efectiva y adaptada a los productos, el stock, los sistemas de almacenaje y preparación de pedidos y, por supuesto, al diseño y características del propio layout.
En Toyota Material Handling disponemos de un amplio catálogo de carretillas elevadoras de gran calidad y dotadas de la mejor tecnología. Además, nuestras posibilidades de personalización son casi ilimitadas. Por este motivo, estamos en disposición de ofrecerles los elementos de manutención y la tecnología que mejor se adapten a cada una de las zonas y áreas de su centro de distribución.