El picking hoy en día es uno de los términos más conocidos en la gestión intralogística del almacén y hace referencia a la actividad de preparación de pedidos, que consiste desde la recepción del pedido, así como la combinación de materias hasta la generación del mismo.
Este proceso puede ser llevado a cabo casi en cualquier tipo de almacén y se desarrolla siempre que sea necesario la unificación de cajas, piezas, materias o productos para su envío.
Conozcamos a continuación más en detalle, qué es y cómo se desarrolla el picking así como cuándo resulta interesante automatizar este proceso operativo.
¿Qué es el picking?
El picking por lo tanto, consiste en la actividad de recolección de ítems para la preparación de pedidos. Esta actividad puede suponer hasta un 55%-60% de los costes de un centro de distribución. En general, la calidad de la operación de picking tiene un impacto tanto sobre la satisfacción del cliente, como sobre la reputación del negocio y su rentabilidad.
Las principales características de una actividad de picking y las relativas tecnologías son las siguientes:
- Escalabilidad: Posibilidad de escalar fácil y rápidamente.
- Flexibilidad: Posibilidad de responder a escenarios cambiantes.
- Precisión y rápida curva de aprendizaje.
- Fiabilidad, especialmente durante picos de trabajo (Black Friday, Campaña de Navidad, etc.)
¿Qué factores influyen en el picking?
El picking es una actividad compleja y multifacética que se ve afectada por una variedad de factores que pueden influir significativamente en su eficiencia y efectividad. Entre los factores más determinantes se encuentran:
-
Diseño del almacén: La disposición física del almacén, incluyendo la ubicación de los productos y la organización de las estanterías, puede afectar directamente la rapidez y precisión con la que se realiza el picking. Un diseño optimizado puede reducir el tiempo de desplazamiento y facilitar el acceso a los productos.
-
Tecnología utilizada: La implementación de tecnologías avanzadas, como sistemas de gestión de almacenes (SGA), escáneres de códigos de barras, y sistemas de picking automatizados, puede mejorar la precisión y velocidad del proceso de picking, reduciendo errores y aumentando la productividad.
-
Capacitación del personal: La experiencia y formación de los operarios de picking son cruciales. Un personal bien capacitado puede realizar el picking de manera más eficiente, minimizando errores y mejorando la satisfacción del cliente.
-
Volumen y variedad de productos: La cantidad de SKUs (unidades de mantenimiento de stock) y la diversidad de productos en el almacén pueden complicar el proceso de picking. Un mayor número de productos y variedad puede requerir estrategias de picking más sofisticadas para mantener la eficiencia.
-
Demanda y estacionalidad: Los picos de demanda, como los que ocurren durante eventos especiales o temporadas de alta actividad (por ejemplo, Black Friday o Navidad), pueden poner a prueba la capacidad del sistema de picking. La flexibilidad para adaptarse a estos cambios es esencial para mantener un servicio eficiente.
-
Precisión y velocidad requeridas: Dependiendo de las expectativas del cliente y la naturaleza del negocio, puede ser necesario priorizar la precisión sobre la velocidad, o viceversa. Esto influirá en la elección de la estrategia de picking y las tecnologías empleadas.
-
Costos operativos: Los costos asociados al picking, que pueden representar una parte significativa del presupuesto de un centro de distribución, también son un factor importante.
Tipos de picking
1. Single Order Picking
En esta estrategia, los pedidos se preparan uno a uno. Cada picker o operario encargado de este procesprocesa las líneas de los pedidos de manera individual. Esta es la solución más simple de picking, que supone bajos costes de implementación. Es adecuada para negocios pequeños ya que se considera una solución poco escalable debido a que un desarrollo notorio del negocio mediante la aplicación de esta estrategia, podría acabar generando un tráfico excesivo en los pasillos.
La curva de aprendizaje de este tipo de estrategia de Picking suele ser lenta, debido a que los operarios tienen que conocer la ubicación de los productos. Además, no se suelen realizar comprobaciones sobre los productos una vez finalizada la preparación de pedidos, lo que podría resultar en errores en la entrega de pedidos.
2. Cluster Picking
Esta estrategia se basa en realizar a la vez la preparación de pedidos diferentes separando los diversos ítems en contenedores separados. La ventaja de este tipo de picking es que el tiempo necesario para el desplazamiento de los operarios se reduce respecto al Single Order Picking, con un consecuente incremento de la productividad del proceso. Por contra, los mismos inconvenientes mencionados anteriormente para el Single Order Picking también aplican al Cluster Picking.
3. Batch Picking
En esta modalidad, se realiza el picking de los Ítems para diferentes pedidos a la vez, pero en lugar de recolectarlos directamente sobre el contenedor final, los productos son depositados sobre un contenedor común a todos los pedidos en preparación. Al final del proceso, los artículos se reparten entre los varios pedidos.
Esta estrategia es recomendada cuando una SKU puede ser incluida en múltiples pedidos. La productividad, comparada con el Single Order Picking, es mayor (mayor número de líneas preparadas en el mismo tiempo), ya que el tiempo necesario para alcanzar las diferentes ubicaciones se distribuye entre diferentes líneas.
Sin embargo, los artículos necesitan de una clasificación a posteriori, lo que resulta en una doble manipulación. Por dicha razón el Batch Picking se suele asociar a equipos de clasificación automáticos.
4. Zone Picking de cajas completas
En esta tipología, cada operario encargado del picking es asignado a una zona de trabajo, en la que recogerá las unidades necesarias para completar las líneas correspondientes a dicha área. El tiempo de desplazamiento para llegar a la ubicación de picking es menor comparado con estrategias tradicionales. El tiempo de preparación para pedidos grandes es menor, y la curva de aprendizaje resulta más rápida.
Esta estrategia se asocia habitualmente a sistemas de transporte automatizado y a un SGA, Sistema de Gestión de Almacén, por lo que requiere de una inversión inicial.
5. Zone picking con order sortation
Esta solución es utilizada cuándo el pedido necesita de picking de ítems a nivel individual (unidades sueltas) en lugar de cajas completas. Se distribuyen contenedores de pedidos al principio de la línea y se distribuye por todas las estaciones que disponen de las SKUs necesarias para el pedido. Del mismo modo que en el zone picking de cajas completas, los operarios siguen trabajando en una zona dedicada, con las ventajas anteriormente mencionadas.
6. Goods to person (G-t-P)
En esta estrategia, las estaciones de picking contienen los pedidos a preparar en lugar de los productos a recoger, al contrario que en el zone picking. Los artículos son transportados hasta las estaciones de picking por un sistema automatizado, dónde se realiza la preparación de pedidos por parte de los operarios.
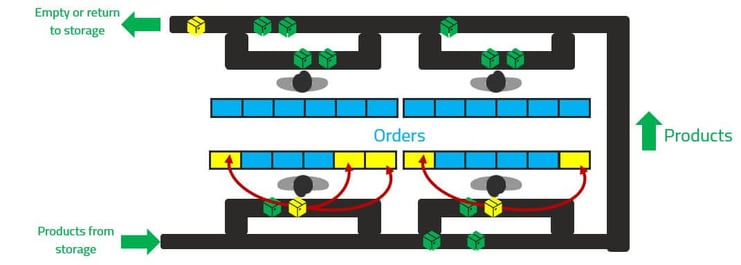
Esta solución es altamente escalable, mediante la implementación de estaciones adicionales, y es muy eficiente debido a que los operarios no necesitan desplazarse para alcanzar los productos.
Generalmente se asocian a estrategias para reducir posibles errores (por ejemplo, básculas). Los productos con los que se preparará el pedido pueden estar almacenados en ASRS (almacenes automatizados), lo que resultaría en una reducción de la mano de obra necesaria. La inversión asociada a estos sistemas suele ser más elevada comparado con otros sistemas, especialmente cuando se emplean tecnologías de ASRS.
Sistemas de picking automático
Cuando nos referimos al picking automático, hablamos de la implementación de sistemas que se encargan de todas las etapas de preparación de pedidos: desde la extracción de mercancía, su transporte dentro del almacén hasta su empaquetado y expedición.
¿Debería automatizar mi actividad de picking?
Las razones para decantarse por una solución automatizada para el picking son diferentes, a continuación resumimos algunas de ellas:
- Conseguir escalabilidad del negocio
- Incrementar volúmenes sin incremento de mano de obra
- Reducir el espacio ocupado en el almacén
- Reducir los errores
- Reducir el lead time a clientes
La importancia representada por la consecución de uno o más de los objetivos mencionados, acompañada por el cálculo del ROI, indicará si es oportuno automatizar la operación de picking en cada caso concreto.
Tecnologías y equipos de picking en almacenes
Detallar las herramientas clave para optimizar el picking en almacenes, como los sistemas de gestión de almacenes (SGA) para una planificación eficiente, lectores de códigos de barras y carretillas preparadoras de pedidos es importante, veamos algunas de ellas.
Carretillas y equipos de picking
El proceso de preparación de pedidos puede llevarse a cabo de manera completamente manual, pero es mucho más eficiente y rentable hacerlo con la ayuda de un preparador de pedidos o mediante soluciones automatizadas más avanzadas, como los robots de picking. Estas máquinas pueden realizar la preparación de pedidos de manera automática y programada. El sistema de preparación de pedidos, también conocido como picking, es una etapa esencial en la que se seleccionan y recogen los productos del almacén para ser organizados, embalados y enviados a los clientes. La eficiencia en esta fase es crucial para garantizar una entrega exitosa de los pedidos.
Sistemas Pick-to-Light y Pick-to-Voice
Se trata de un sistema de picking que utiliza estanterías dinámicas y visores numéricos para guiar al operario en la localización y cantidad de artículos a recoger. El visor, gestionado por el sistema de Gestión de Almacenes (SGA) indica al operario la ubicación exacta y el número de unidades a recolectar. El operario procede a recoger, escanear y confirmar la acción, lo que apaga la luz indicadora. Para nuevos pedidos, las luces se activan automáticamente. Los sistemas pick-to-light son especialmente adecuados para almacenes con alta carga de trabajo en espacios reducidos y con productos de fácil manipulación.
Software de Gestión de Almacenes (SGA)
El Sistema de Gestión de Almacenes (SGA) es un software que automatiza los procesos y las actividades diarias de un almacén en cada etapa logística, desde la recepción de mercancías hasta su almacenamiento, preparación y envío de pedidos. Es una herramienta fundamental para optimizar todas las operaciones del almacén y mejorar la eficiencia. Su relevancia se debe a su capacidad para rastrear los materiales del almacén y facilitar la selección y empaquetado de productos por parte de los empleados.
¿Qué estrategia de picking se adapta mejor a mi negocio?
Para definir la mejor estrategia de picking para un negocio, es necesario mirar a los datos de la operación:
- Número de SKUs
- Mix de productos
- Tipo de formato: pallets enteros, capas, cajas, fracciones o mix
- Tamaño y layout del centro de distribución
- Distribución de pedidos: tamaño del pedido, cantidad de SKUs y características
- Tipo de entregas: retail, e-commerce, omnichannel
Una vez analizados los datos, estos se convierten en inputs para el diseño de la solución más adecuada en cada caso, para proceder sucesivamente con el cálculo del nivel de inversión y del ROI asociado.
Beneficios del picking optimizado y cómo Toyota puede ayudarle
A lo largo del artículo, hemos destacado la relevancia de un picking optimizado, el cual ofrece una serie de beneficios que se detallan a continuación.
- Optimizar los desplazamientos de los operarios mediante un diseño eficiente y una estrategia de zonificación adecuada. Reducir el número de operaciones y el tiempo necesario para su ejecución.
- Lograr una precisión absoluta en las operaciones (Zero Muda).
- Mantener una rotación de inventario precisa, considerando criterios como FIFO/LIFO, y asegurar un control constante mediante un sistema de gestión de almacenes (SGA).
- Mejorar el control presupuestario. Reducir los costos operativos.
En Toyota Material Handling, proporcionamos soluciones especializadas para la optimización de las operaciones de picking.
Nuestras máquinas recogepedidos son compactas, estables y adecuadas para uso intensivo en diversos entornos. La dirección electrónica asegura maniobras rápidas y precisas. Toyota ofrece configuraciones estándar de portacargas, garantizando movimientos seguros. Construidas bajo el sistema TPS, aseguran calidad y durabilidad.
Maximiza la productividad con los Recogepedidos Toyota; Los recogepedidos Toyota tienen configuraciones variadas y pueden personalizarse según necesidades. Mejoran la efectividad operario-máquina y la productividad. Su rendimiento optimizado permite control seguro y flexibilidad. La función t-mote aumenta la productividad y mejora la ergonomía, reduciendo la fatiga del operario.