Cuando hablamos de stock de seguridad nos referimos al inventario extra que muchas empresas tienen en su almacén, para hacer frente a imprevistos como retrasos de los proveedores o posibles cambios en la demanda.
La principal ventaja de contar con este margen razonable de existencias es que evita la rotura de stock.
¿Qué es el stock de seguridad?
El stock de seguridad es la cantidad adicional de artículos que una empresa reserva estratégicamente en su almacén con el objetivo de mitigar el riesgo de quedarse sin existencias en momentos críticos. Esta reserva adicional de inventario se considera una medida preventiva para hacer frente a imprevistos como retrasos en las entregas de los proveedores o cambios repentinos en la demanda del mercado.
Importancia del stock de seguridad
Es de vital importancia, ya que garantiza:
- Asegura la continuidad de las operaciones al mantener los niveles de inventario necesarios para satisfacer la demanda.
- Reduce los efectos negativos de huelgas, retrasos en las entregas y otros inconvenientes en la planta.
- Responde de manera efectiva al aumento en la demanda.
- Mejora la eficiencia en la distribución de los artículos.
- Reduce el riesgo de dañar la reputación debido al desabastecimiento.
¿Cómo se calcula el stock de seguridad?
Para calcular el stock de seguridad es necesario seguir fórmulas matemáticas que combinan las diferentes variables que influyen en este valor.
Aunque no existe una única fórmula para calcular cuál es el stock de seguridad más adecuado para una empresa, una de la más utilizada es la siguiente:
Stock de seguridad = (Máximo plazo de entrega - Plazo habitual de entrega) x Demanda media del producto
Conviene señalar que el cálculo del stock de seguridad se realiza cada vez de forma más automática. Habitualmente mediante un SGA (software de gestión de almacén) que incluye esta función.
Otro método muy utilizado y práctico, consiste en considerar el stock de seguridad como un porcentaje del stock de maniobra. Para considerar dicho porcentaje se tienen en cuenta los históricos de ventas y la previsión de la demanda (forescating).
Aplicación del Modelo Wilson en la gestión del stock
El Modelo de Wilson o Sistema EOQ (Economic Order Quantity, que en castellano puede traducirse por cantidad de lote económico) se basa en determinar con precisión la cantidad y el costo de cada pedido, evitando así aproximaciones. Esto permite evitar gastos innecesarios o errores matemáticos. Es un modelo fácil de utilizar e implementar, lo que constituye una de sus mayores ventajas y la razón principal de su popularidad.
La utilidad básica del modelo Wilson es que permite calcular cada cuánto y en qué cantidad hay que realizar un pedido a un proveedor, garantizando así una adecuada gestión de stock.
Estrategias para optimizar tu stock de seguridad
Para un calcular un stock de seguridad óptimo se deben tener en cuenta estos factores clave:
Mejores prácticas para gestionar el stock de seguridad en almacenes
- Establecer el tiempo de entrega ¿Cuánto tiempo tardará el proveedor en entregar los productos una vez realizado el pedido?
- Evaluar la variabilidad de la demanda ¿Es posible que su producto tenga éxito? ¿O tiene una demanda constante?
- Calcular el nivel de servicio
- Aplicar la fórmula adecuada para determinar el stock de seguridad
Uso de software de gestión de inventarios para mejorar la precisión
Un SGA o Software de Gestión de Almacenes (en inglés WMS, siglas de Warehouse Management System) es un sistema diseñado para gestionar, coordinar y optimizar todas las operaciones y procesos de un almacén. El SGA es crucial en la logística moderna, ya que apoya toda la organización y gestión de los almacenes. Aunque en logística se habla frecuentemente del flujo físico de mercancías, el flujo de información es igualmente importante, ya que permite conocer en todo momento la ubicación y estado de cada producto. Un flujo de información fluido, detallado y confiable solo se puede lograr con un buen software de gestión de almacenes y su uso adecuado.
Consejos para evitar rotura de stock y excedentes
- Conocer con el mayor detalle posible cuál es nuestra situación actual
- Controlar el ciclo de vida de cada producto
- Utilizar las herramientas tecnológicas que permiten prever la demanda y controla el stock
- Realizar un mantenimiento adecuado de equipos e instalaciones
- Hacer una previsión de la demanda con márgenes de error adecuados
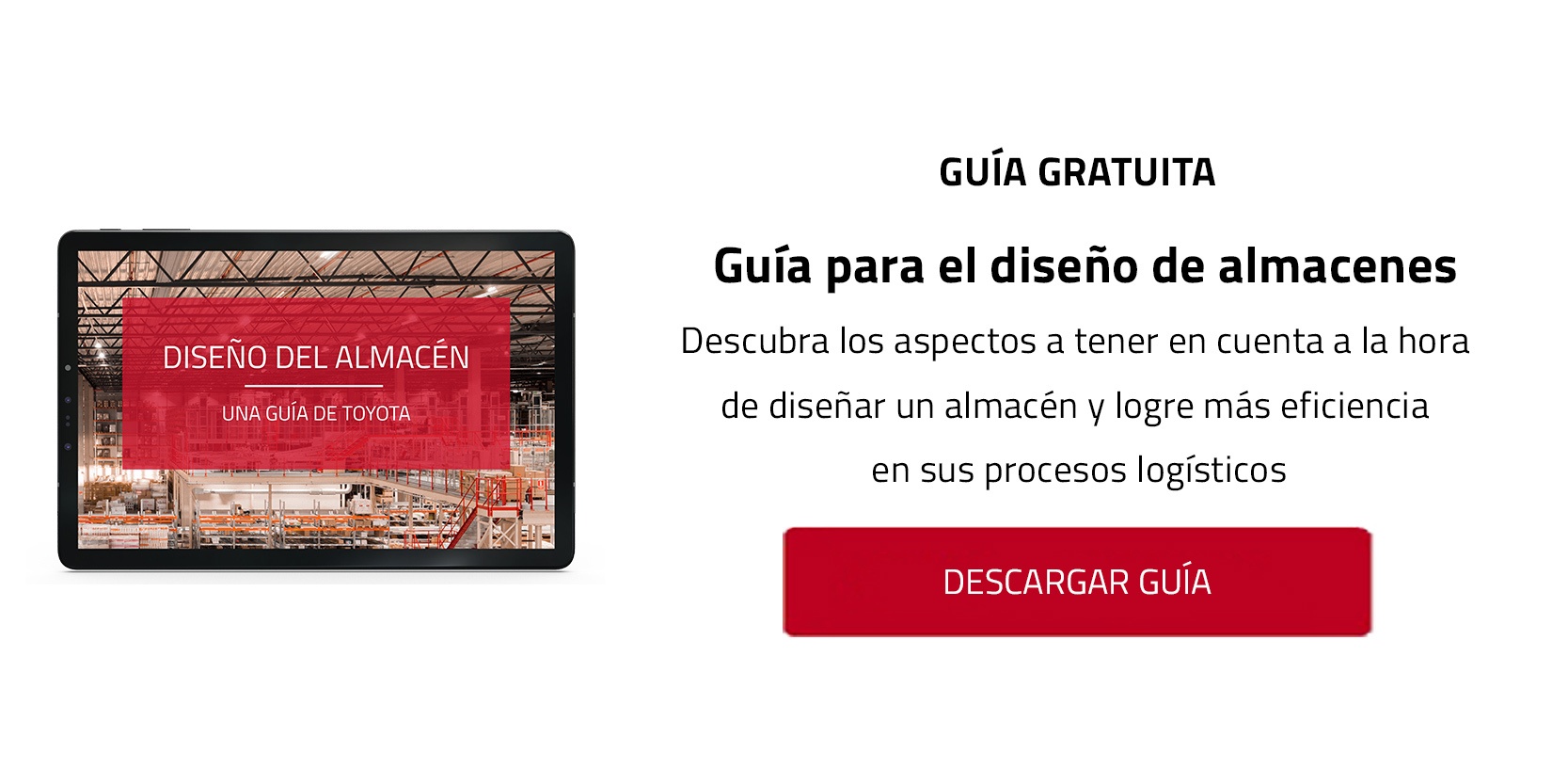
Ventajas del stock de seguridad
Para comprender la dimensión, importancia y alcance del stock de seguridad, es importante conocer los principales factores o variables que influyen en él:
1. Variaciones de la demanda
Aunque actualmente la mayoría de empresas utilizan estrategias de previsión de la demanda para la regularización del stock de seguridad, en ocasiones el consumo es difícil de controlar, debido a circunstancias cómo:
-
El surgimiento de nuevos productos.
-
El peso de la competencia.
-
Las fluctuaciones del mercado.
-
La estacionalidad de muchos productos.
2. Nivel de servicio de la empresa
Se considera que un empresa tiene un nivel de servicio adecuado cuando es capaz de satisfacer plenamente la demanda de sus clientes. Es decir, tener un buen nivel de servicio significa que el almacén puede suministrar el producto que piden los clientes en el momento en que lo necesitan, sin que se produzcan retrasos por una rotura de stock.
Cada empresa, de acuerdo con su política comercial, debe determinar y conocer qué nivel de servicio debe proporcionar a sus clientes. Para ello debe tener en cuenta cómo se comporta la competencia y si su nivel está por encima o por debajo del nuestro.
3. Tiempo de reacción de suministros por parte de los proveedores (lead time)
Se denomina lead time al tiempo estimado que tarda un proveedor en suministrar al almacén los productos pedidos. Por lo general, las empresas acuerdan con sus proveedores un tiempo de suministro concreto. En ocasiones, su incumplimiento puede derivar en sanciones e, incluso, en la finalización del contrato de colaboración.
Es importante elegir proveedores capaces de reaccionar ante imprevistos, como por ejemplo unas condiciones meteorológicas adversas, que cuenten con alternativas y soluciones de emergencia. Es primordial es que el cliente reciba su mercancía a tiempo, o con el mínimo retraso posible.
Optimización del stock, uno de los puntos fuertes de Toyota
Uno de los grandes logros y aportaciones de Toyota al sector industrial, en su sentido más global, ha sido acuñar y poner en práctica el método conocido como TPS o Toyota Production System.
La comprobada efectividad del sistema TPS y el método Just In Time (justo a tiempo) para optimizar la logística y la producción, reducir costes y lograr la mejora continua con cero errores, ha provocado que, desde hace ya décadas, empresas de todos los tamaños y sectores opten por adaptarlo e implantarlo.
El TPS se caracteriza por buscar el equilibrio en almacenes y fábricas, intentado mantener el stock de seguridad siempre en el nivel justo para poder satisfacer, en todo momento, la demanda de los clientes, incluso ante situaciones imprevistas. En todo momento, se intenta evitar llegar a situaciones de acumulación de stock, que podrían cuestionar la eficacia del trabajo y aumentar los costes logísticos.